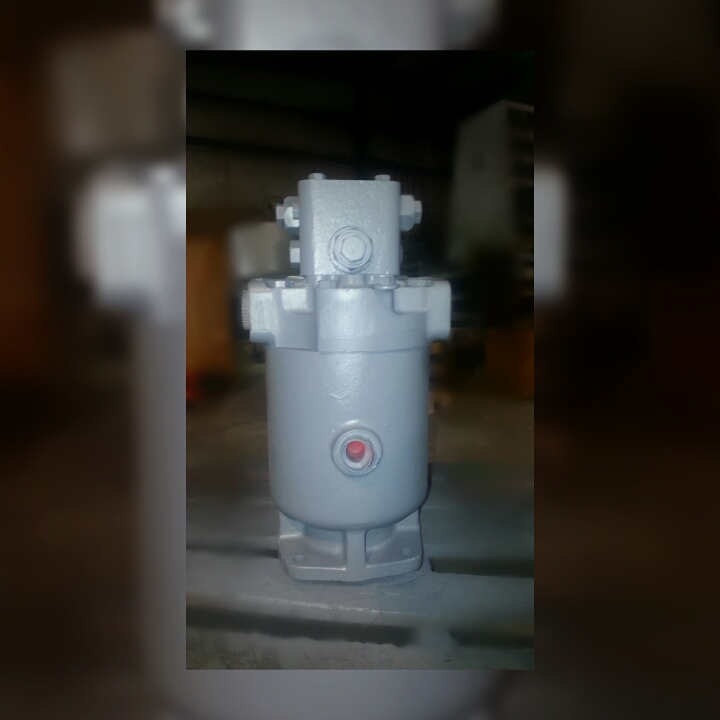
A. Put in two dowel pins and a gasket on the end cover, make sure to put grease on the bearing shims and cup before you put them in the end cover.
B,D & E. You will need to look at the end play of your output drive shaft. Put in the end cover so that you don’t put in the valve or bearing plates. It gets rid of the need for a spring tension going up against the output shaft. Put in cap screws in the end cover and tighten them up evenly. Next goes the support motor assy. on the end cover. Slightly tap the output shaft a hammer or something like it. The magnetic base indicator goes next on the mounting flange with the gauge on the output shaft end. Pliers or something like it to get ahold of of the output shaft as low as you can. You will need to pull upwards to see how much play you have in the shaft end. It usually needs to stay within .002 – .007 inches of play. If it is not set right, you can fix it by adding or taking away shims under the bearing cup.
C. Once you get it like you want it, put the motor on the mounting flange and take off the end cover. Put in the dowel pins in front of cylinder barrel subassy. Put grease on bearing plate with the dowel pins and put it in the cylinder barrel.
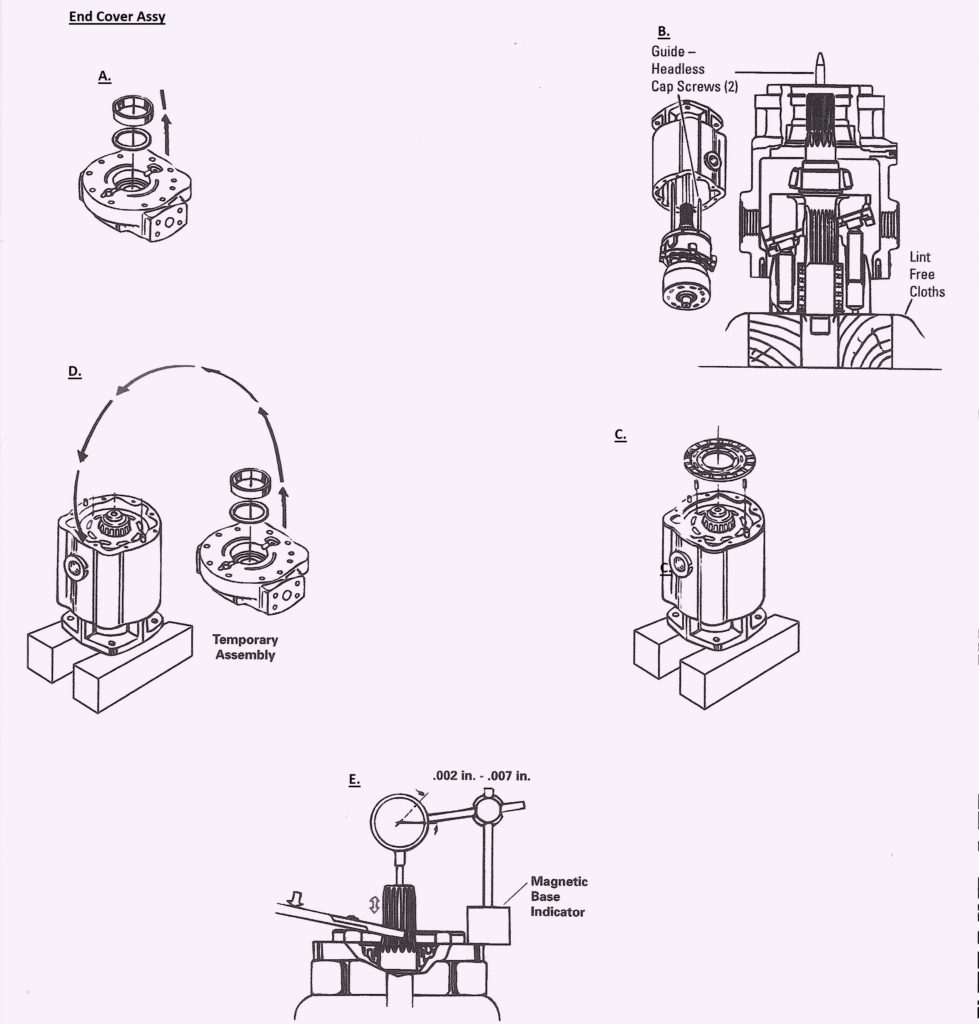
If you need questions answer about this or if we can repair your unit, call us at 800-361-0068
sales@htsrepair.com