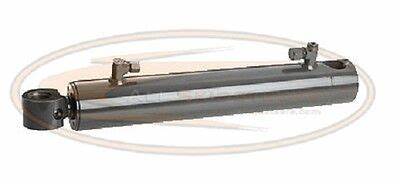
A hydraulic cylinder (also called a linearhydraulic motor) is a mechanical actuator that is used to give a unidirectional force through a unidirectional stroke. It has many applications, notably in construction equipment ( equipment, vehicles) manufacturing machinery, elevators) and civil engineering. A hydraulic cylinder is the actuator or “motor” side of this system. The “generator” side of the hydraulic system is the hydraulic pump which delivers a fixed or regulated flow of oil to the hydraulic cylinder, to move the piston. There are three types of pump widely used: hydraulic hand pump, hydraulic air pump, and hydraulic electric pump. The piston pushes the oil in the other chamber back to the reservoir. If we assume that the oil enters from the cap end, during extension stroke, and the oil pressure in the rod end/head end is approximately zero, the force F on the piston rod equals the pressure P in the cylinder times the piston area
For double-acting single-rod cylinders, when the input and output pressures are reversed, there is a force difference between the two sides of the piston due to one side of the piston being covered by the rod attached to it. The cylinder rod reduces the surface area of the piston and reduces the force that can be applied for the retraction stroke
During the retraction stroke, if the oil is pumped into the head (or gland) at the rod end and the oil from the cap end flows back to the reservoir without pressure, the fluid pressure in the rod end is (Pull Force) / (piston area – piston rod area): P = F p A p − A r {\displaystyle P={\frac {F_{p}}{A_{p}-A_{r}}}}
where P is the fluid pressure, Fp is the pulling force, Ap is the piston face area and Ar is the rod cross-section area.
For double-acting, double-rod cylinders, when the piston surface area is equally covered by a rod of equal size on both sides of the head, there is no force difference. Such cylinders typically have their cylinder body affixed to a stationary mount.
Tie rod style hydraulic cylinders use high strength threaded steel rods to hold the two end caps to the cylinder barrel. They are most often seen in industrial factory applications. Small-bore cylinders usually have 4 tie rods, and large bore cylinders may require as many as 16 or 20 tie rods in order to retain the end caps under the tremendous forces produced. Tie rod style cylinders can be completely disassembled for service and repair, and they are not always customizable.
Welded body cylinders have no tie rods. The barrel is welded directly to the end caps. The ports are welded to the barrel. The front rod gland is usually threaded into or bolted to the cylinder barrel. That allows the piston rod assembly and the rod seals to be removed for service.
Welded body cylinders have a number of advantages over tie rod-style cylinders. Welded cylinders have a narrower body and often a shorter overall length enabling them to fit better into the tight confines of machinery. Welded cylinders do not suffer from failure due to tie rod stretch at high pressures and long strokes
The welded design also lends itself to customization. Special features are easily added to the cylinder body, including special ports, custom mounts, valve manifolds, and so on.[11]
The smooth outer body of welded cylinders also enables the design of multi-stage telescopic cylinders.
Welded body hydraulic cylinders dominate the mobile hydraulic equipment market such as construction equipment, excavators, bulldozers, and road graders) and material handling equipment (forklift trucks, telehandlers, and lift-gates). They are also used by heavy industry in cranes, oil rigs, and large off-road vehicles for above-ground mining operations.
A differential cylinder acts like a normal cylinder when pulling. If the cylinder however has to push, the oil from the piston rod side of the cylinder is not returned to the reservoir but goes to the bottom side of the cylinder. In such a way, the cylinder goes much faster, but the maximum force the cylinder can give is like a plunger cylinder. A differential cylinder can be manufactured like a normal cylinder, and only a special control is added.
The above differential cylinder is also called a regenerative cylinder control circuit. This term means that the cylinder is a single rod, double-acting hydraulic cylinder. The control circuit includes a valve and piping which during the extension of the piston, conducts the oil from the rod side of the piston to the other side of the piston instead of to the pump’s reservoir. The oil which is conducted to the other side of the piston is referred to as the regenerative oil.
Call us today for more help in repairing cylinders
662-871-8403
tupelohydraulics@gmail.com